At BW LPG, we are three quarters into our Safer Together Program – a new initiative which has set the course for how we work towards our vision of Zero Harm. Under this initiative, colleagues go in-depth into a main topic each quarter and have monthly meetings to develop a deeper understanding of the important issues that are faced at the workplace.
From teamwork and leadership, to care, and to risk
We kicked off the year with discussions around teamwork and leadership, because we depend on each other at BW LPG to succeed. In the second quarter, we reminded colleagues that we care , and showed the many ways this care is manifested. We also focused on psychological safety at work, and emphasized that mental health is just as important as physical health onboard at the workplace. This quarter, our focus shifts to the topic of Dealing with Risks. At the workplace, we can be surrounded by hazards, or potential sources of injury. We must ensure that we introduce and maintain barriers between us and the potential harm from hazards. If a mistake is made, we must be prepared to control resultant risks, because without that control, we may get hurt, and that is unacceptable. In Q3, we therefore focused on risks and learnt strategies to keep ourselves safe.
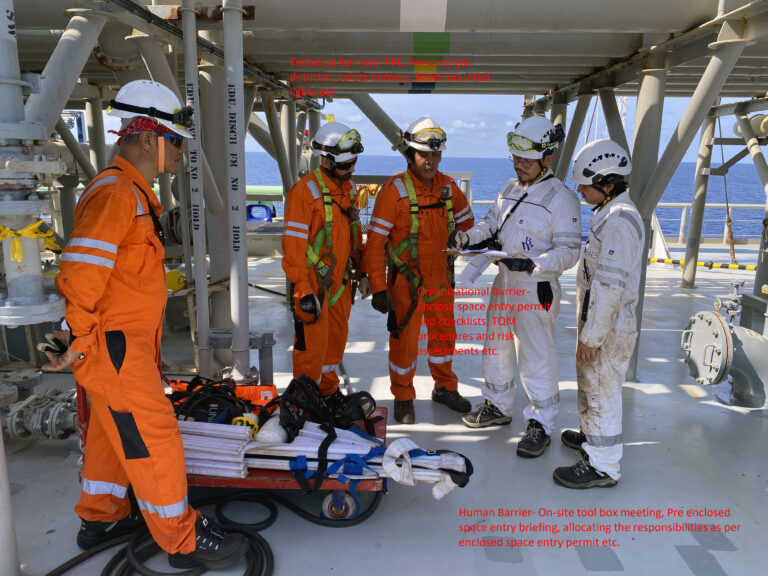
Risk is all around
At BW LPG, we deliver cleaner-burning energy to world markets. This means that we have a unique workplace where we manage the transportation and storage of flammable, pressurized products; products which are vital to power economies and communities. It also means that we must have processes in place to deal with inherent risks.
Dealing with risks means doing our best to reduce the chance of injury by controlling hazards around us. We have different strategies to control the risks we face. We follow established rules and procedures, we use a hierarchy of controls to establish barriers such as emergency shutdowns, or physical barriers against rotating parts, or in the last instance the use of personal protective equipment (PPE). We are also trained to have the right level of competency for the tasks at hand.
Golden rules for process safety
We follow rules, regulations and guidelines when performing tasks, because these keep us safe as we work on critical systems. They serve as reminder of what we need to check and keep in mind to stay safe when performing certain tasks.
Build up barriers
Protective measures can shield us from harm, either by absorbing or diverting hazards. We can also eliminate or remove hazards, modify the risk profile through substitution, and engineer controls to protect ourselves from harm. Procedures are there to provide safe work guidelines, and if incidents happen, our PPE such as gloves, helmets and safety goggles can mitigate consequences.
Training and competency
Proper knowledge to acquire a standard of competency to complete the tasks at hand can reduce potential for injury, especially when complex equipment is involved.
Be prepared for changes
We know the common adage that “the only constant is change”. How can we deal with risks, as we work in ever-changing scenarios and situations? The simple answer is to stop, and think. Colleagues are taught to ask, “Is what I am currently doing safe?”. If he or she is uncertain, the next step is to check again, and not hesitate to ask for verification or assistance. Everyone in the company has the right to issue a Stop Work Order – Any delay is worth it if we avoid injury.
We are glad to see very practical suggestions from our crew onboard – from focusing on “buddy checks” to help reassess risks, to allocating more time to plan for tasks and discuss expected and unexpected events that may happen during operations. Below is a safety observation from crew onboard Very Large Gas Carrier BW Brage.
“During ongoing maintenance of windlass, it was observed that one of the crew members was trying to climb up on the windlass without a safety harness. This is unsafe and the team immediately used our stop work authority and advised the crew member to use a harness. This observation clearly identifies the importance of teamwork and how looking out for oneself and each other can help us avoid hazards.”
At BW LPG, we encourage all colleagues on shore and at sea to embrace the program and do our part for Zero Harm. Because our efforts will be repaid in personal growth, a better working environment and improved safety for all of us. Nothing else matters if we do not bring our team members home safely.
Keywords: HSEQ, health, safety, ESG, social, workplace, culture, values at work, safety culture, just culture, maritime, shipping, energy, LPG, sustainability
Read More
- Read our Q2 article on “I Care About You”
- Read our Q1 article on “Safer Together: As Easy As ABC”
- Read about our approach to Health and Safety